Screen printing is one of the important technology of solar cell manufacturing, its quality will be important influence on performance, especially the performance of solar cells.In solar cell production process, through diffusion system, plasma etching to go around
And PECVD system to reduce the membrane technique, the next process is mainly formed good electrode contact, which is completed jointly by silk screen printing and sintering process.
Silk screen printing itself is a traditional industrial technology, it has been widely used since the seventy s.Because of its low requirements for equipment, and has obvious advantages in lower production costs, so the technology is also widely used in solar cell production.Secondly, using the screen printing process can be carried out large-scale production and reduce production cycle.Again, use the screen printing can reduce pollution, avoid the photolithography, corrosion and other such waste more process.In recent years, through the improvement of silk screen printing process, greatly improve the standards of the process, can be grid line width to around 50 microns, film thickness increased to 20 microns, through improvements on slurry, make the solar cell parameters are improved obviously.
7.1 the working principle of silk screen printing
Printing electrode solar cells, the first is made of vacuum evaporation or chemical plating technology is now widely used silk screen printing method, namely through the special printing machine and templates to silver pulp, aluminum paste printing on the back of the sun, the batteries are, in order to form positive and negative electrode, lead again after baking at low temperature, high temperature sintering, solar cells can be obtained finally.In the back of the solar cell electrode is simpler, can be combined with a thin layer of metal on the back of the whole layer, in order to easy to welding, when necessary to a layer of tin plating.But the positive of the battery must ensure that transparent to the light, as a result, the battery positive electrode comb shaped, wire mesh or dendritic structures.The form of positive electrode and the thickness is always the result of two factors balance: on the one hand to have high transmittance;On the other hand as much as possible to ensure the reseau electrode has a low contact resistance.To this, the pv manufacturers have many different production process.Often cell positive (negative) comb electrode structure, generally speaking, there are 2 or 3 main electrode thick line, in order to connect the welding, and often on the back with aluminum silicon alloy as a back surface field, in order to improve the open circuit voltage, the back (the anode) there are 2 or 3 for welding thick electrode lines, and often also is full of fine grid line.
Figure 7.1 for a polysilicon solar cell surface, which can see the main gate of two vertical line and a lot of cross fine grid line, these are the result of the silk screen printing and sintering.
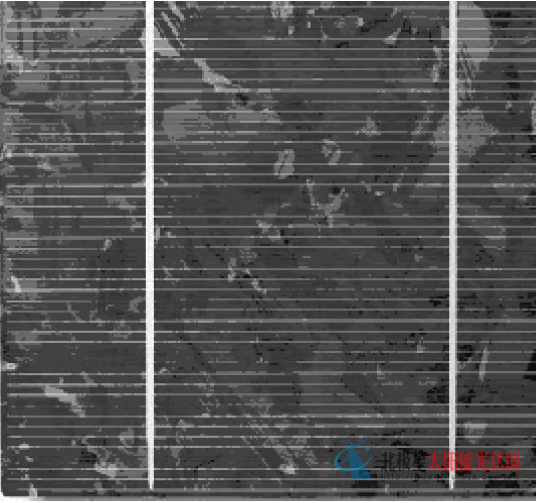
The surface of the polycrystalline silicon solar cell diagram in figure 7.1
Silk screen printing by the five elements, namely, silk screen, scraper, pulp, workbench, and substrate.Basic principle is: screen printing paste using silk screen graphics part of the mesh, the graphic part of the mesh is not through the basic principle of paste for printing.In silk screen printing at one end into pulp, with scraper in a certain pressure paste parts of the screen, the screen at the same time the other end of the move.Ink scraper from graphics in mobile extrusion in the part of the mesh to the substrate.Due to the effect of viscosity of the slurry and the imprinting fixation within a certain range, the scraper is always in the process of printing and silk screen printing and printing substrates in line contact, the contact line with scraper and movement, because the silk screen and keep some space between the substrates, when the silk screen printing by tension and reaction of scraper, the reaction is called elastic back.Due to back to the effect of elastic silk screen and substrate only show mobile line contact, and other parts of the screen and substrates for out of the state, ensure the dimensional accuracy and avoid smearing printing substrates.When scraper scrape up after the printing area, and also from the substrate, screen workbench is returned to the feeding position, at this point for a printed itinerary.Request control the movement of the fluid in the process of silk screen printing, printing, silk screen on the slurry leakage due to high viscosity flow themselves a screen;When printing, scraper slurry pressure into the hole, under the action of scraper and silk screen, paste was very shear stress and viscosity drops rapidly through the mesh, so as to contact with the substrate.In the process of the silk screen rebound adhesion to the substrate (as shown in figure 7.2).
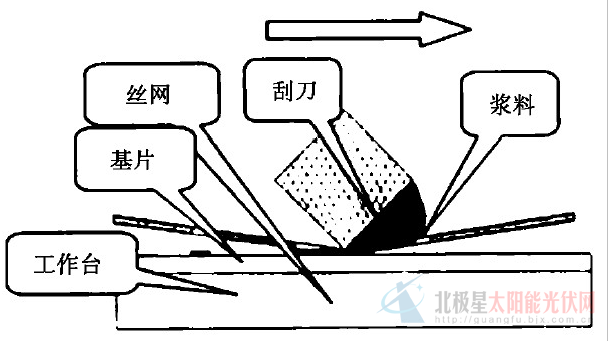
Figure 7.2 the principle diagram of the silk screen printing
7.2 the structure of automatic and semi-automatic screen printing equipment and main technology characteristics
7.2.1 automatic screen printing equipment structure and main technical characteristics
Figure 7.3 for automatic screen printing equipment.Solar printing line is newly developed for silicon solar cell production lines set automatic feeding, automatic printing, automatic transmission, automatic drying and automatic transmission assembly line printing drying system (figure 7.4).
The main technical characteristics:
1. The feeding mechanism: material box of rotary mechanism for 6 station, one can load 240 substrates.
2. Printing: scraper adopts servo motor drive, precision helical screw transmission;Printing pressure precision is adjustable.Screen frame with the X, Y, Z, theta adjustment function.
3. The transmission mechanism: driven by stepping motor synchronous cog belt transmission, transmission smooth;
The main technical indicators:
1. The production efficiency: 800 ~ 1000 / hour;
2. Suitable for single crystal substrate or polycrystalline 125 mm * 125 mm;
3. On the way: material box automatic feeding;
4. Area: 3700 mm (l) x 2700 mm (w) x 1500 mm (h);
5. Power supply: AC380V / 50 hz, 230 kw.
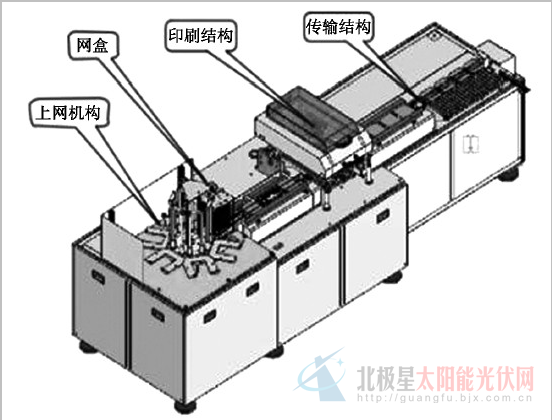
Automatic screen printing equipment schematic diagram in figure 7.3
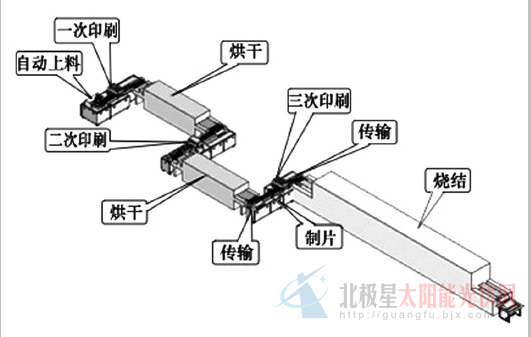
7.2.2 semi-automatic screen printing equipment structure and main technical characteristics
Here is China's production of a semi-automatic printer (WY - 216 type precision visual registration screen printing press) (as shown in figure 7.5).WY - 216 type precise visual registration screen printer product biggest printing size is 8 inches, it is mainly used for electricity
The following device in the fruit industry of high precision graphic printing: solar cell, thick film circuit, PCB, LCD, SMT, ceramic substrates and filters, magnetic components, etc.
The main technical characteristics:
1. Adopt servo motor drive, precision guide screw drive, grating feet feedback full closed loop control, accurate positioning.X, Y, theta and Z to have fine tune, X, Y, theta direction changed from micrometer head, Z motion driven by cylinder, four sets of precision guide pin guide bush guide and adjust high precision.
2. Servo motor drive, precision ball screw drive, precision linear guide the guidance, the printing process of uniform motion in a straight line;Scraper Angle is adjustable;Printing pressure and ink coating pressure adjustable, respectively, the stress classification compensation technology, make the printing pressure constant, and with the instrument shows.
3. The diagonal is realized by using two sets of CCD system positioning, and displayed on the monitor positioning results;Adjust the workbench to make graphics with graphic example, intuitive, convenient and high alignment accuracy.
4. Net box flip system: net box flip driven by cylinder, chain drive to complete, easy to clean net.
The main technical indicators:
1. The printing area: Max210mm x 210 mm;
2. Net frame shape size: 356.4 mm x 356.4 mm x 25.4 mm500mm x 500 mm x 25 mm;
3. The workbench repeat accuracy: + / - 0.01 mm;
4. The scraper and physical activity: 0 ~ 10 mm;
5. Printing stroke: 50 to 250 mm (adjustable);
6. The workbench speed: 10 ~ 500 mm/s (adjustable);
7. The scraper speed: 0 ~ 350 mm/s (adjustable);
8. The workbench adjustment quantity: X, Y: + / - 5 MMZ: 0 ~ 5 mm theta: plus or minus 3 °;
9. Printing pressure: 0.1 ~ 0.3 MPa;
10. The scraper Angle adjustment: 0 ~ 30 ° (adjustable);
11. The compressed air source: 0.5 MPa;
12. The power supply: AC220V50Hz;
13. The whole machine power: 1.1 kW.
14. Overall size: 1200 mm * 1000 mm * 1500 mm;
15. The weight: about 800 kg.
7.3 silk screen printing equipment operation and safety codes
In general, silk screen printing in three times to complete, the flow chart as shown in the figure 7.6.
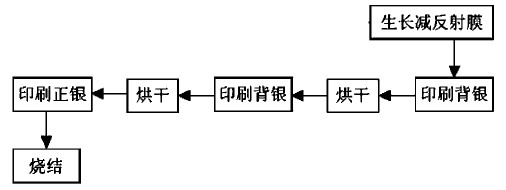
A common printing flow chart in figure 7.6
The operation of 7.3.1 silk screen printing equipment
1. The scraper parallelism
(1) single dynamic state, the platform into the side, above print head movement to the platform.
(2) loosen the lock cylinder mother, lift knob, close to the platform, the macroscopic observation scraping and platform of parallelism.
(3) adjust the parallelism, lock handle release first, by adjusting the knob to adjust the scraper with parallel platform.
(4) after the adjustment, lock the handle.
2. Adjust the screen height (if necessary)
(1) horizontal plate, the print head movement to the side, the workbench in the movement to the side.
(2) the machine in the open state.
(3) the front support shaft handle, loosen the support shaft in the free state.
(4) pull (plate rack up/down button, at the same time observe behind on both sides of the dial indicator.
(5) after the adjustment, lock the handle of the support shaft.
3. To screen
(1) tie the frame before open, press "plate rack flip" button, the print head gently lift.
(2) adjust: loosen the screen frame in the first two lock handle, adjust the knob on the right side, dial indicator, adjustable control position, adjusted the lock handle.
(3) before and after the adjustment, loosen the screen frame in the first two lock handle, adjusting plate in front of the two knobs at the same time, the control dial indicator, adjustable front and rear position, adjusted the lock handle.
(4) the Angle adjustment: loosen the first two lock handle, screen frame table plate frame (also can be adjusted at the same time), the front two knob control dial indicator, adjustable Angle, adjusted the lock handle.
4. Adjust the printing pressure
(1) on the operation panel/single action automatically switch to single action.
(2) the platform in the movement to the side, the print head movement to the platform.
(3) place the paper above the platform, resulting in a print head.
(4) loosen the lock cylinder mother, adjust the scraper increase/decrease switch, to a certain tension can pull the paper can, locking cylinder lock.
7.3.2 silk screen printing equipment safety standards
1. Enter the workshop must wear good purification clothing, hats, wearing masks, gloves, hair long to put it in the hat and clothes.
2. The gowning at least once every two weeks cleaning, work shoes also want regular scrubbing, check regularly.
3. The succession team must arrive 20 minutes early workshop, responsible for production line of health work, including cleaning the ground, the trash, wash pulp mixing platform, mesh belt, clean up the debris, etc.
4. The wafer to light with light.
5. In silicon and halftone screen printing contact clean gloves production personnel must be replaced.Between different printing process to avoid operator string hillock, avoid cross contamination.If necessary, clean gloves must be replaced.
6. Platform holes to dredge on a regular basis.
7. Platform sticky paste, dip in with the clean cloth to wipe clean with alcohol;Then clean dust-free cloth on it, open the continuous adsorption, rear can normal printing and repeat several times.
8. Each replacement screen, screen location, printing pressure and scraper parallelism to readjust.
9. Each process should be timely fill out fragments statistics;In principle, the wafer broken if will affect the printing of the next working procedure, the silicon wafers as pieces processing.If you don't affect the printing of the next working procedure, this is not a process will be recorded in the debris.
Silicon wafer broken 10. Printing process, the application will be at the bottom of the screen and platforms to wipe clean.
11. Put a piece of printing platform, once put in place as far as possible, don't put silicon friction on the platform.
12. Back electrode printing, the operator must check into the silicon wafer to see if there is any breakage, the number is consistent with the process card, once found the problem, inform the captain, and registration on the process card.
13. Once the back electrode have been phenomenon occurred, should immediately stop printing, and find the reason too little (size, mesh plug).
14. Aluminum back printing field, to periodically sheet on pulp, generally will be subject to seal a box, of course on the screen size, more frequently and scraping;Don't wait for the wafer scraping printing defects.
15. Aluminum back field were drying, calls for "the thumb contact back field, and other four fingers contact positive" way to insert or piece of work, to avoid cross contamination.
16. Splicing personnel cannot meet the slice wear cotton gloves, PVC gloves or just use PE gloves splicing.
17. The positive electrode printing, should be regularly with a clean cloth graze the bottom of the screen, avoid too thick grid line.
18. The access way of silicon and aluminum back field drying splicing, same requirement the thumbs touch back.
19. Pay attention to the direction of printing, positive electrode to the main grid line and back electrode in the same direction.
7.4 silk screen printing equipment maintenance and maintenance
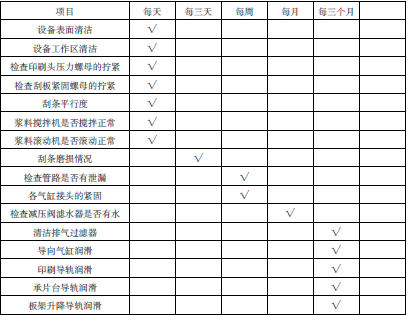
7.5 the development direction of silk screen printing equipment
Fully automatic screen printing machine, automatic FenJianJi peace plate PECVD three kinds of equipment such as technique entirely dependent on imports, domestic demand in the near future but corresponding domestic equipment launch day has been.Automatic print head products are developing more, the key technology is a breakthrough, the machine into the market and accepted by the user needs a period of time, manual and semi-automatic unable to enter the mainstream product line.
The current domestic manufacturing photovoltaic mainly manual and semi-automatic screen printing machine, fully automatic screen printing technology is not yet mature, silk screen printing machine automatic is inevitable.In addition, advanced screen printing template with nickel plate laser groove is made, to ensure the durability of the template and the precision of the grid.General screen printing on the front of the electrode is about 7% for the light shade, USES the advanced template printing process can reduce the light shade, and a certain degree of lower contact resistance at the same time, make the battery efficiency will be improved.